|
|
|
Fachpraxis
Hauptmotivation für die Teilnehmer war die pure Freude am Arbeiten, das "Hineinschnuppern" in die Arbeitstechniken eines Metallbearbeiters, sowie das Lernen in einem für sie bisher völlig unbekannten Umfeld.
Hier nun die Techniken, die zum Bau unserer Wurfmaschine verwendet wurden:
|
|
Berechnen
Unter einer Berechnung versteht man die Ermittlung eines Zahlenwertes nach den Regeln der Mathematik. Berechnungen können einfache Aufgaben sein, wie die Berechnung des Preises beim Einkauf von Nahrungsmitteln oder komplexe Aufgaben bis hin zu Flugbahnen, Wahrscheinlichkeiten u.a.m. die heute meist mit Hilfe von Computern durchgeführt werden. |
|

Berechnung...
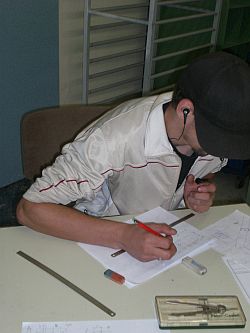
Konstruktion...
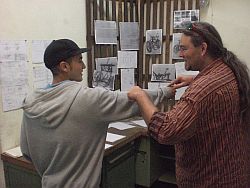
Das Hebelgesetz...
|
|
Zeichnen
Eine Technische Zeichnung ist ein Dokument, das in grafischer Form alle notwendigen Informationen für die Herstellung eines Einzelteils, einer Baugruppe oder eines kompletten Produkts zeigt. Die Technische Zeichnung ist das Ergebnis des Prozesses Technisches Zeichnen. |
|
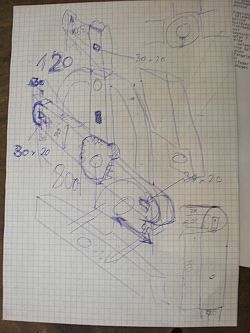
Erste Skizzen...
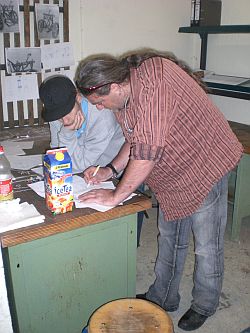
Tommy erklärt das...
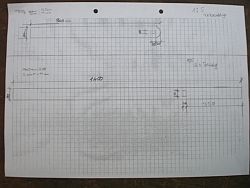
Die erste Technische Zeichnung...
|
|
Anreißen
Als Anreißen wird die Tätigkeit des Übertragens von Maßen auf ein Werkstück bezeichnet. |
|
|
Sägen
Die Säge ist ein Werkzeug zum Trennen von Holz, Naturstein, Metall, Kunststoff und anderen festen Materialien. Sie besteht aus einer dünnen, am Rand mit meißelartigen Zähnen versehenen Stahlplatte, dem Sägeblatt, die durch eine Kraft bewegt wird und mit den Zähnen in das Innere des Körpers eindringt und durch Wegnahme dünner Späne (Sägespäne) eine schmale Nut in den Körper einarbeitet und so die Trennung herbeiführt. Je nachdem, ob das Sägeblatt mit der Hand oder mit Maschinenkraft bewegt wird, unterscheidet man zwischen Handsägen und Maschinensägen (oder Sägemaschinen). Die Säge ist ein zerspanendes Werkzeug. Eine kontinuierliche Bewegung der Sägezähne findet man beispielsweise an einer Kreissäge und eine diskontinuierliche bei den Handsägen wie dem Fuchsschwanz.
Um ein Festklemmen des Sägeblattes im Werkstoff zu verhindern, muss der Schnitt breiter sein als das Sägeblatt. Dies erreicht man *durch ein gewelltes, gestauchtes oder geschränktes Sägeblatt. Bei einem gewellten Sägeblatt sitzen die einzelnen Zähne nicht auf einer geraden Linie, sondern laufen in leichten Kurven. Gestauchte Zähne sind an der Zahnspitze breiter. Bei einem geschränkten Sägeblatt sind die Zähne abwechselnd nach rechts und links gebogen. Heute findet man häufig auch eine Bestückung des Sägeblatts mit einem anderen Material, etwa Hartmetall, das dann entsprechend breiter ist als das Blatt. |
|
|
Feilen
Feilen ist eine meist manuelles, seltener maschinelles Fertigungsverfahren um ein Werkstück in geringem Maße zerspanend zu formen. Feilen zählt zu den spanenden Trennverfahren mit geometrisch bestimmter Schneide.
Umgangssprachlich wird der Ausdruck auch benutzt um auszudrücken, dass an einem Objekt (auch an einem Menschen) letzte Verbesserungen durchgeführt werden. Mit einer Feile werden nahezu alle Metalle, Holz und Kunststoffe mechanisch zerspanend bearbeitet, aber auch an verhornte Körperteile wie Nägel und Hufe wird die Feile angelegt. |
|
|
"Flexen"
Ein Winkelschleifer (auch Trennschleifer, Trennjäger, Trennhexe, Schleifhexe, Feuerradl; ein bekannter Markenname ist FLEX) ist eine elektrische Handmaschine mit schnell rotierender runder Schleifscheibe. Die Firma Ackermann + Schmitt (FLEX-Elektrowerkzeuge GmbH), die als „Erfinder“ des Winkelschleifers gilt, hat den Markennamen FLEX eingeführt. Beim Winkelschleifer wird die Schleifscheibe über ein Winkelgetriebe angetrieben, welches dem Winkelschleifer seinen Namen gibt. Weitere bekannte Markenhersteller von Winkelschleifern sind AEG, Bosch, Fein, Makita und Metabo.
Das runde Werkzeug rotiert mit bis zu 12.000 Umdrehungen pro Minute (bei 115 mm Scheibendurchmesser) und ist daher hohen Fliehkräften ausgesetzt. Die theoretische Schnittgeschwindigkeit der Scheiben am Umfang liegt üblicherweise bei ca. 80m/s, die Leerlaufdrehzahlen der für unterschiedliche Scheibendurchmesser (üblich sind: 115, 125, 150, 180, 230 und 300 mm, letzteres nur als Trennschleifer) gebauten Maschinen unterscheiden sich entsprechend. Um ein Zersplittern oder Bersten des Werkzeugs zu vermeiden, sind die Scheiben durch Gewebeeinlagen verstärkt und besitzen dank einer besonders elastischen Kunstharzbindung eine gewisse Flexibilität im Vergleich zu starren Schleifscheiben (Schleifstein) oder Flachschleifmaschinen. Diese Flexibilität ermöglicht ein manuelles, freihändiges Trennschleifen von Metall, Stein und anderen Werkstoffen, ohne dass die Schleifscheibe im Falle einer leichten Verkantung zerbricht. |
|
|
Schleifen
Schleifen ist ein abtragendes, wegbestimmtes Fertigungsverfahren zur Bearbeitung von Oberflächen mit Schleifmitteln, manuell oder auf Schleifmaschinen. Nach DIN 8580 gehört es zur Hauptgruppe Trennen. Außerdem gehört es zu der Gruppe der Zerspanungsarten mit geometrisch unbestimmter Schneide.
Die Vorzüge des Schleifens gegenüber anderen Arten der Zerspanung sind die gute Bearbeitbarkeit harter Werkstoffe, die hohe Maß- und Formgenauigkeit (IT 5-6) und die geringe Welligkeit und Rauheit (Rz= 1-3μm) der geschliffenen Oberfläche.
Die Körnungsnummer entspricht der Maschenzahl des Siebes auf 1 inch Länge, durch welches das bezeichnete Korn gerade noch hindurchfällt, während es auf dem nächstengeren Sieb liegen bleibt. Die sehr feinen Körner werden im Schlämmverfahren getrennt. Die Körnungen von Diamant und Bornitrid werden entsprechend der Siebmaschenweite in μm angegeben (Diamantkorn D150 - hat eine Korngröße zwischen 125 μm und 150 μm). |
|
|
Bohren
Ein Bohrer, auch Bohr-Einsatz genannt, ist ein Werkzeug oder Werkzeugteil zum Erzeugen kreisrunder, seltener vieleckiger Löcher in ein Material durch Zerspanen. Das entstehende Loch wird Bohrung genannt.
Das Verfahren selbst heißt Bohren und zählt in der Ordnung der Fertigungsverfahren auf Grund der definierten Schneide zu den Trennverfahren mit geometrisch bestimmter Schneide. |
|
|
Drehen
Drehen ist ein zerspanendes Fertigungsverfahren für Metalle und Kunststoffe. Gedreht wird manuell auf einer Drehbank oder automatisiert auf einer Drehmaschine. Im Gegensatz zum Fräsen dreht sich hier das Werkstück beziehungsweise Halbzeug; es führt die Hauptschnittbewegung mit seiner Rotation aus. Das fest eingespannte Werkzeug (Drehmeißel) wird am drehenden Werkstück mit Hilfe des Werkzeugschlittens entlang bewegt, um einen Span abzuheben; es führt die Zustell- und Vorschubbewegung aus. Nur in besonderen Fällen (beispielsweise bei Gewindewirbeln) trägt auch das Werkzeug zur Schnittbewegung bei.
In der Einteilung der Fertigungsverfahren nach DIN 8580 zählt das Drehen als Trennverfahren.
Beim klassischen Drehen werden hauptsächlich rotationssymmetrische (runde) Teile bearbeitet. Die moderne Technologie einer CNC-Drehmaschine macht es möglich, auch Werkstücke zu fertigen, die früher nur auf einer Fräsmaschine zu produzieren waren. |
|
|
Fräsen
Fräsen bezeichnet das spanabhebende Bearbeiten von Metallen, Holz oder Kunststoffen mittels eines Fräswerkzeuges. Es erfolgt auf speziellen Werkzeugmaschinen – in der Regel Fräsmaschine oder Bearbeitungszentrum.
Im Gegensatz zum Drehen wird die zur Spanabhebung notwendige Schnittbewegung durch Rotation des Schneidewerkzeuges gegenüber dem fest im Maschinentisch eingespannten Werkstück erzeugt. Die hingegen zur Formgebung notwendige Vorschubbewegung wird je nach Bauart entweder durch Verschiebung des Maschinentisches oder durch Bewegung des Fräswerkzeuges um das Werkstück herum erreicht. Vorschubbewegungen können je nach Bauweise – auch kombiniert – in der X- ,Y- und Z-Achse oder entlang der jeweiligen Rotationsachsen erfolgen.
In der Einteilung der Fertigungsverfahren nach DIN 8580 zählt das Fräsen als Trennverfahren. |
|
|
Schweißen
Unter Schweißen versteht man gemäß DIN 1910-1 (DIN 1910-1 wurde durch DIN ISO 857-1 ersetzt) das unlösbare Verbinden von Bauteilen unter Anwendung von Wärme oder Druck – mit oder ohne Schweißzusatzwerkstoffen.
Besonders häufig werden Schmelzschweißverfahren für meist metallische Materialien angewendet, jedoch auch für Glas (bei Gebrauchsprodukten oder bei Glasfasern in der Nachrichtentechnik) sowie für thermoplastische Kunststoffe. Die Verbindung erfolgt je nach Schweißverfahren in einer Schweißnaht oder einem Schweißpunkt, beim Reibverschweißen auch in einer Fläche. Die zum Schweißen notwendige Energie wird von außen zugeführt.
Schmelzschweißen ist Schweißen bei örtlich begrenztem Schmelzfluss ohne Anwendung von Kraft mit oder ohne gleichartigem Schweißzusatz (DIN ISO 857-1). So kann man unter anderem Metalle, Thermoplaste oder Glas verschweißen.
Das Material kann nach nach dem Schweißen und dem Abkühlen nachteilige Eigenschaften aufweisen (Aufhärtung, Versprödung), was durch Materialwahl, Atmosphäre und Verfahren vermieden werden muss.
Beim Schmelzschweißen von Stahl ist zu beachten, dass nur bei einfachen Stählen mit einem Kohlenstoffgehalt bis 0,22 % C (Festigkeit 500 N/mm²) ohne weiteres dauerhafte Schweißverbindungen zustande kommen. Bei höherfesten und legierten Stählen sind, um Rissbildung und Brüchen vorzubeugen, Zusatzmaßnahmen erforderlich, z. B. Vorwärmen, langsames Abkühlen, Anlassen, Spannungsarmglühen, oder es müssen spezielle Schweißverfahren angewendet werden.
Der Zweck des Schweißens wird unterschieden nach Verbindungs- und Auftragsschweißen. Verbindungsschweißen ist Fügen (DIN 8580) eines Werkstückes, z. B. Rohrlängsnaht. Auftragsschweißen ist Beschichten (DIN 8580) eines Werkstückes durch Schweißen. Sind der Grund- und der Auftragswerkstoff artfremd, wird unterschieden zwischen Auftragsschweißen von Panzerungen, Plattierungen und von Pufferschichten. |
|
|
Schmieden
Schmieden ist das spanlose Umformen von Metallen zwischen zwei Werkzeugen. Es wird von Schmieden betrieben.
Beim Warmschmieden wird das zu schmiedende Halbzeug in einem Ofen erwärmt, im Gegensatz zum Prägen wird dabei der gesamte Werkstoffquerschnitt plastifiziert. Durch dieses Erwärmen verändert sich die Kristallitstruktur des Werkstoffs, und das Material wird weicher. Messing, Bronze, Kupfer, Edelmetalle und deren Legierungen werden dagegen in der Regel kalt geschmiedet. |
|
|
Biegen
Biegen ist ein umformendes Fertigungsverfahren, dabei wird auf das Material ein Biegemoment aufgebracht und somit eine plastische das heißt dauerhafte Verformung herbeigeführt. |
|
|
Spachteln
Ein Spachtel ist ein Handwerkzeug welches in vielfältiger Art und Weise benutzt werden kann.
Mit Spachteln können nicht nur Werkstoffe breiiger Konsistenz (z.B. Spachtelmasse) verarbeitet werden. Man verwendet sie je nach Art bei vielen handwerklichen Tätigkeiten, z. B. auch zum Ablösen von flächigen Werkstoffen, wie Tapeten. Sie werden jedoch hauptsächlich zum Auftragen, Verteilen und Glattstreichen des Materials verwendet. |
|
|
Lackieren
Mit Oberflächenbehandlung werden technische Verfahren bezeichnet, bei denen in erster Linie die äußeren Schichten des zu behandelnden Teils bearbeitet werden. |
|
|
Montage
Als Montage in der industriellen Fertigung bezeichnet man den planmäßigen Zusammenbau von Bauteilen und/oder Baugruppen (Module) zu Erzeugnissen (Produkte) bzw. zu Baugruppen höherer Erzeugnisebenen. Die Umkehrung der Montagetechnik ist die Demontage mit entsprechenden Demontagetechniken. Die wesentlichen Teiloperationen eines Montageprozesses sind:
Fügen (z. B. Schweißen)
Handhaben (z. B. Greifen)
Kontrollieren (z. B. Messen)
Justieren (z. B. Einstellen)
Sonderoperationen (z. B. Reinigen)
Die Montage bildet neben den Bereichen Arbeitsvorbereitung, Teilefertigung/-bearbeitung und Fertigungsteuerung einen Teil des Produktionssystems eines Industriebetriebes.
Die Montage wird in zwei Arten unterschieden:
Primärmontage ist das Fügen der Bauteile.
Primärmontagevorgänge sind alle Vorgänge, die der Wertschöpfung eines Produktes während des Montagevorganges dienen.
Sekundärmontage umfasst das Handhaben, Kontrollieren, Justieren und Sonderoperationen. |
|
|
|
|
|
|
|